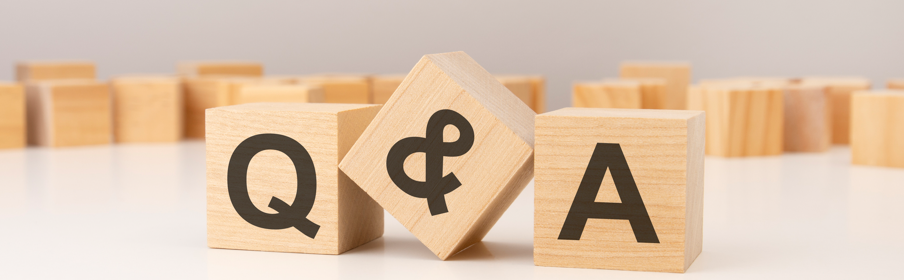
Below you will find frequently asked questions about the integrity assurance of single-use systems. A print friendly version is available to download here.
These questions have been reviewed and answered by BPSA’s Integrity Assurance Committee of industry experts.
Additional Questions: If you have additional questions, you can submit them to bpsa@socma.org. Inquiries will be reviewed by BPSA’s Committee, and the most relevant questions will be added to the FAQ page.
Expert Level Rating: Each FAQ is assigned an expert level rating based on its technical complexity, as determined by the Committee. The expert level rating ranges from Basic level*, Medium level***, and Expert level*****.
Updates/Versions: The FAQs are periodically updated based on further information and feedback from the Committee. This will be indicated by the version number and date listed under each FAQ.
Additional BPSA Resources:
- BPSA Technical Guide, 2023 Design, Control and Monitoring of SUS for Integrity Assurance, Volume 2
- BPSA Technical Guide, 2017 Design, Control and Monitoring of SUS for Integrity Assurance
Level: ** | Version 1, September 2024
Technically, some of the established test methods used for pre-use testing, such as pressure decay or flow rate measurement, can be applied post-use as well. There is however a risk of false PASS, as residual liquid/product (liquid or dried) in the SUS can impact the test result, e.g., due to blocking a defect in the SUS (also refer to Table 2 in ASTM E3244).
This also applies to helium tracer gas in sniffer mode. Helium tracer gas detection in vacuum mode is nearly impossible to apply post-use, as the evaporation of residual liquid would highly impact the generation of an appropriate vacuum level, unless the system is carefully dried. This is a complex operation that limits this post-use test to specific validation testing.
For all test methods to apply it reliably post-use, a prerequisite would be to establish a validated cleaning and drying procedure for the SUS, bringing it back to the state as it was before use.
Note that there are simple good practices expected to be in place to check for the absence of leaks during the process, such as visual checks with or without aids (see section 3.5, third paragraph of the BPSA Technical Guide, Volume 2, for further details)
When the test is considered to be an integrity test (not a leak test), the sensitivity of the test method must be established (see section 5.1 of the BPSA Technical Guide, Volume 2, for further details)
ASTM E3244-20, Standard Practice for Integrity Assurance and Testing of Single-Use Systems.
BPSA Technical Guide, 2023 Design, Control and Monitoring of SUS for Integrity Assurance, Volume 2
Level: ** | Version 2, Updated March 2025
When pressure for the leak/integrity test is applied on a SUS (for both pressure decay, and tracer gas detection), the surface areas of the test article that are mechanically supported by the container wall (or other supporting structures) are pressed against the structure surface. This can cause the blocking of a potential defect in this surface area, also called masking effect. More considerations about masking effect can be found in ASTM E3244-23, Table 2 and E3336-22 5.2.2.2 Note 8).
ASTM E3244-23, Standard Practice for Integrity Assurance and Testing of Single-Use Systems
ASTM E3336-22, Standard Test Method for Physical Integrity Testing of Single-Use Systems
Level: * | Version 2, Updated March 2025
Introduction of particulate matter, microorganisms (bioburden), moisture or oil residues are not acceptable for single-use applications. Compressed air used for pressure decay leak testing shall be produced in a manner that delivers oil free, dry air, free from particulate matter. It is best practice to additionally fit the test system with a sterilizing grade point of use filter in the flow path directly before the test article. It should be noted that the sterilizing grade filter must not be used to compensate for compressed air of poor quality. Further, the sterilizing grade filter will not deliver sterile air if it has not been previously sterilized.
Level: * | Version 1, September 2024
Integrity and leak testing of single-use systems (SUS) encompass a spectrum of tests that may be employed to ensure integrity assurance as part of a quality by design approach. Most commonly pressure decay and tracer gas leak tests are used to establish the integrity of SUS or specific components in a non-destructive manner. The test methods are developed to ensure the SUS is not damaged by the testing due to over pressurization, contamination or other means. These efforts during test method development and validation help to ensure no final drug product is lost as a result of the failure of the tested SUS or contamination of the SUS. A validation package showing the absence of impact of the leak/integrity test on the CQA (Critical Quality Attributes) of the SUS is expected to be generated by the supplier.
Further details on validation expectations associated to pressure based test methods and tracer-gas based test methods can be found in ASTM E3336-22.
Some destructive leak tests may be employed during validation or as lot release tests. Examples include microbial ingress testing or bubble leak tests. In these instances, the SUS or component subjected to the testing is not expected to be used for the end-use application.
ASTM E3336-22, Standard Test Method for Physical Integrity Testing of Single-Use Systems
Level: ** | Version 1, September 2024
This is a very important distinction, as it has a direct impact on the SUS assurance of integrity. “Integrity test” is still too often misused to name a simple leak test.
Physical testing of SUS can only provide a full integrity guarantee when the detection limit can be correlated to the barrier properties of the SUS.[2]
Barrier properties are defined according to the intended use or process compatibility of the SUS[1], maintaining the adequate barrier between the inside and outside of the SUS. Examples would be transparency to light, barrier to microbial ingress, to liquid loss or gas permeability.[1]
According to the common definitions in ASTM E3244, E3251 and E3336, only a test method with a limit of detection good enough to confirm the barrier properties of a SUS is an integrity test. A test method with inferior (less performant) or unqualified limit of detection is only a leak test.[2]
An integrity test is usually correlated to the size of an orifice/hole, which is itself correlated to the intended barrier property or Maximum Allowable Leakage Limit (MALL). See BPSA Technical Guide, Volume 2, section 5.1 for further details on MALL.
A leak test acceptance criterion can be associated to a leak size, but without the correlation to the MALL. Another typical example of leak test acceptance criterion is the maximum delta pressure allowed in case of pressure decay leak testing.
[1] BPSA Technical Guide, 2017 Design, Control and Monitoring of SUS for Integrity Assurance, section 2.2.1
[2] BPSA Technical Guide, 2023 Design, Control and Monitoring of SUS for Integrity Assurance, Volume 2, section 5.1
Level: * | Version 1, March 2025
The decision to perform (or not) a leak or an integrity test at the point-of-use should be based on Contamination Control and operational risk assessments. The level of risk depends on several factors, e.g. the criticality of the process, the technical feasibility of doing the test, safety hazards of process fluids, and the balance between risk mitigation and additional risks due to the test.
Suppliers can help end users to evaluate integrity/leak testing methodology, test sensitivity, and single use system designs to support integrity testing. More discussion can be found in section 3.6 of the BPSA Technical Guide, Volume 2.
BPSA Technical Guide, 2023 Design, Control and Monitoring of SUS for Integrity Assurance, Volume 2
Level: *** | Version 1, March 2025
A test performed at the end user site will assess additional steps of the SUS lifecycle, such as packaging, shipping from the supplier site to the end user site, handling steps such as unpacking and set up.
When relying on testing at the supplier site, close attention must be given to elements covering subsequent steps of the lifecycle of the SUS, e.g. shipping validation (typically in accordance with ISTA standards), visual controls performed prior to use (typically following a “Single-Use Visual Observation Library” – see sections 6.3 and 7.2.4 of the of the BPSA Technical Guide, Volume 2) and repeatable, gentle handling procedures. Complexity of the controls increases with the criticality of the application and associated end user integrity control strategy.
From a technical perspective, most currently available physical test technologies can be applied at the supplier site as well as at the end-user site. However, several aspects may limit the use of specific technologies at either site (see Table 1 in ASTM E3244-23):
- Helium tracer gas technology is very complex, expensive, difficult to maintain and requires working under vacuum for optimized sensitivity. It may not be reasonable to implement such a technology at the end user site for only testing a low amount of SUS. For a SUS manufacturer, the barriers of implementing tracer gas technology may be outweighed by superior sensitivity and acceptable cycle time. Properly managing a sophisticated test method such as Helium integrity testing requires expert resources in the organization.
- Testing by pressure decay is fairly easy for a SUS manufacturer. It is more complex at end user level, presenting design limitations and constraints as well as specific risks. Moreover, it does not generally offer the sensitivity for an integrity test correlated to microbial ingress, even with an extended test time. See section 3.6 of the BPSA Technical Guide, Volume 2 for more detailed considerations. Note that, for some specific cases, pressure decay can reach a 10 µm sensitivity, which is correlated to a microbial challenge by aerosol. See section 5.4.1 of the BPSA Technical Guide, Volume 2 for more details.
BPSA Technical Guide, 2023 Design, Control and Monitoring of SUS for Integrity Assurance, Volume 2
ASTM E3244-23, Standard Practice for Integrity Assurance and Testing of Single-Use Systems
Level: * | Version 1, March 2025
As explained in FAQ 5 “What is a difference between a leak test & an integrity test?“, an integrity test is used to confirm the barrier properties of the single use system. It must be correlated, directly or indirectly, to the ability of the test to detect a breach in the intended barrier while a leak test is used to check the single use system for leaks independent from the barrier properties.
For POU (Point-of-Use) testing technologies available on the market, only leak test exists because of the difficulties to use integrity testing methods such as Helium test in a production area. POU leak test are important to detect leak in case of product dangerous for operators (e.g. concentrated virus solution) or in case of operational risk associated to a major leak (e.g. 1 000L bags) and as business risk to avoid losing production time associated to a leak. However, users should always keep in mind that for pressure decay / flow measurement test methods (typically used for POU testing), the bigger the volume the lower the sensitivity, this means that you essentially see holes with a diameter at the level of millimeters when dealing with large size vessel.
Level: * | Version 1, March 2025
Integrity testing and/or integrity monitoring is expected for sterile manufacturing steps based on Annex 1 request to have a control of integrity for closed systems (§8.130).
For non-sterile applications, an integrity test is not mandatory. Risk of leakage should be evaluated considering potential hazard associated to leak (BL (Biosafety Level) of biologics) or supply time to replace the single-use system. Leak testing is recommended here to minimize such risk, which is higher for single use items complex to manufacture and/or single-use items whose manufacturing process is associated to multiple manual manufacturing steps (such as 3D bags versus 2D bags).
Another important element that can be considered in the risk analysis is the complexity of manipulating the SUS at end user site. For example, frequent manual handling of the bags, operating SUS consistently under dynamic and high pressure or flow condition, and freeze-thaw storage environment. Such elements may lead to implement a leakage test before use to minimize risk of product loss or sterility breach. Implementing such leak testing does not lower the need to follow critical QbD steps: robust design of SUS (including use of qualified junctions) and equipment, processes, and thorough operator training program. These are critical elements that reduce more the risk level than a leak test. Implementing a leak test will lower the risk of leaks but not eliminate it, as a leak test can only detect medium to large leaks (see section 5.4.2 of the BPSA Technical Guide, Volume 2 for more detailed considerations).
BPSA Technical Guide, 2023 Design, Control and Monitoring of SUS for Integrity Assurance, Volume 2
Level: *** | Version 1, March 2025
Suppliers should be prepared to provide information that supports the User Requirements for the system. Users should provide the anticipated process conditions and how they change with time: temperature, pressure, flowrate, and chemical environment. Suppliers should compare their system and/or component test data with the stated process conditions. It is important to understand that some parts of a SUS might be exposed to different maximum operating pressures: for example, in case of leak test or PUPSIT, sub-parts of a SUS are exposed to high pressure when other must be kept under low pressure (typically the bag chamber).
Suppliers should provide test data that confirms that the system will remain integral when used in the proposed operating conditions. Preferably, the tests are made at conditions that are more rigorous than the proposed operating conditions.
If system integrity validation is provided, it is important to compare the conditions of the integrity testing against the user’s intended process conditions. Suppliers should provide information required to calculate the safety margin. The safety margin describes how close the proposed operation is to the test conditions. The required magnitude of the safety margin is decided by the user’s risk assessment.
THESE FREQUENTLY ASKED QUESTIONS (FAQs) ARE PROVIDED BY BIO-PROCESS SYSTEMS ALLIANCE (“BPSA”) FOR INFORMATIONAL PURPOSES ONLY. CLICK TO VIEW FULL DISCLAIMER.
THESE FREQUENTLY ASKED QUESTIONS (FAQs) ARE PROVIDED BY BIO-PROCESS SYSTEMS ALLIANCE (“BPSA”) FOR INFORMATIONAL PURPOSES ONLY. ANY INACCURACY OR OMISSION IS NOT THE RESPONSIBILITY OF BPSA. DETERMINATION OF WHETHER AND/OR HOW TO USE ALL OR ANY PORTION OF THIS DOCUMENT IS TO BE MADE IN YOUR SOLE AND ABSOLUTE DISCRETION. PRIOR TO USING THIS DOCUMENT OR ITS CONTENTS, YOU SHOULD REVIEW IT WITH YOUR OWN LEGAL COUNSEL. NO PART OF THESE FAQs CONSTITUTES LEGAL ADVICE. USE OF THIS DOCUMENT IS VOLUNTARY. BPSA DOES NOT MAKE ANY REPRESENTATIONS OR WARRANTIES WITH RESPECT TO THIS DOCUMENT OR ITS CONTENTS. BPSA HEREBY DISCLAIMS ALL WARRANTIES OF ANY NATURE, EXPRESS, IMPLIED OR OTHERWISE, OR ARISING FROM TRADE OR CUSTOM, INCLUDING, WITHOUT LIMITATION, ANY IMPLIED WARRANTIES OF MERCHANTABILITY, NONINFRINGEMENT, QUALITY, TITLE, FITNESS FOR A PARTICULAR PURPOSE, COMPLETENESS OR ACCURACY. TO THE FULLEST EXTENT PERMITTED BY APPLICABLE LAWS, BPSA SHALL NOT BE LIABLE FOR ANY LOSSES, EXPENSES OR DAMAGES OF ANY NATURE, INCLUDING, WITHOUT LIMITATION, SPECIAL, INCIDENTAL, PUNITIVE, DIRECT, INDIRECT OR CONSEQUENTIAL DAMAGES OR LOST INCOME OR PROFITS, RESULTING FROM OR ARISING OUT OF A COMPANY’S OR INDIVIDUAL’S USE OF THIS DOCUMENT, WHETHER ARISING IN TORT, CONTRACT, STATUTE, OR OTHERWISE, EVEN IF ADVISED OF THE POSSIBILITY OF SUCH DAMAGES.