What Lies Ahead for Single-Use Technology: 2020 Perspectives
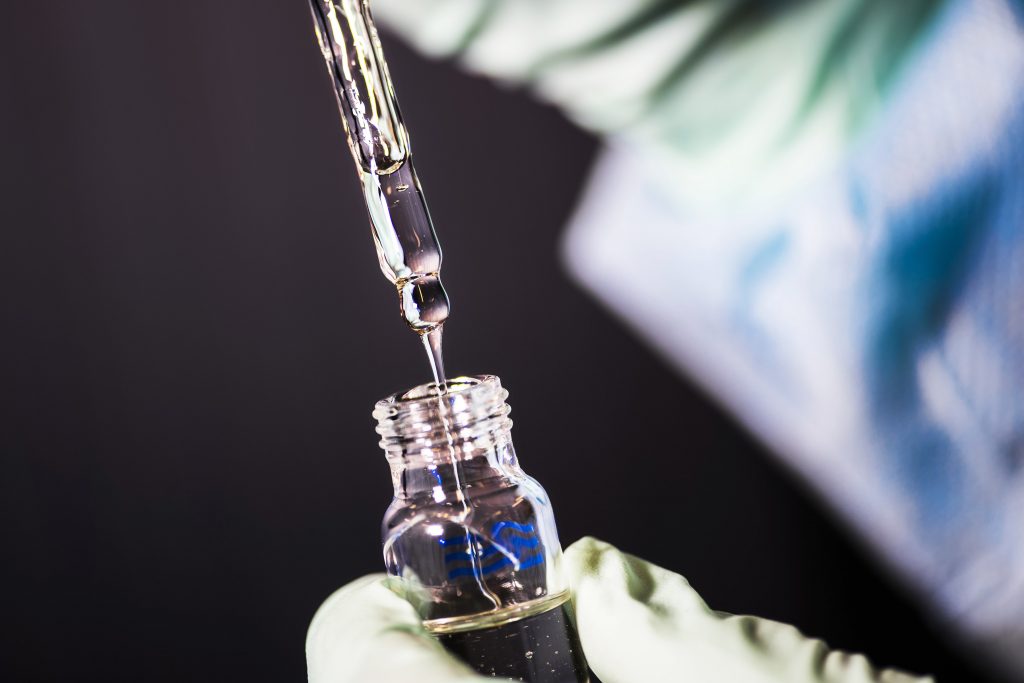
October 14, 2019
October 14, 2019
Single-use technology (SUT) has had a major impact on how precision biologic therapies are manufactured. So, what does the future hold for SUT in a world where single-use plastics are increasingly seen as an “eco-threat” instead of a means to manufacture life-saving therapies? Kevin Ott explains why sustainability is a complicated concept, but one that must be addressed by the single-use industry as we move into the next decade of SUT adoption and growth.
AS AN INDUSTRY group with a presence in both Europe and North America, the Bio-Process Systems Alliance (BPSA) welcomes this opportunity to reflect upon the unprecedented growth of SUT adoption over the past decade. More importantly, for the readers of European Pharmaceutical Review, we would also like to offer a cogent view of what may lie ahead. If “what is past is prologue” there is a robust future for SUTs, provided that innovation, risk management, continuous improvement investments, product enhancements and sustainable practices continue to be implemented.
The BPSA mission
Reflecting a little; since BPSA’s inception in 2005, we have viewed the accelerated be in double-digit CAG territory – and also ‘sustainable’ in the context of its merits adoption of SUTs as a global endeavor. This goal is, and always has been, evident in our mission statement, which remains: “Advancing Single-Use Worldwide”. Though our business presence is based in Washington, DC, a key element of our strategic intent is to be a global industry association, focusing on the key features and benefits of polymer-based bioprocessing.
Looking ahead: sustained SUT growth beyond 2020
Perspectives on what lies ahead can be garnered by addressing the duality of the question: “is single-use sustainable?” The issue of sustainability can be viewed in terms of maintaining its impressive growth and adoption numbers – now estimated to as a high-performance, environmentally friendly alternative or hybrid supplement to traditional steel systems.
The answer in both cases is yes; provided that the industry continues to be problem solvers of the first order – and this includes staying on top of end-user risk mitigation issues and addressing and promoting its environmental sustainability benefits.
Healthy business growth has not been granted to the SUT business because SUTs are new and better – the hard-earned industry growth of SUT is due to consistent and effective industry collaborations (along with international regulatory and standards bodies) that have addressed common problems, or hurdles, to the adoption of SUTs; including managing a paradigm shift from steel to polymers – a significant and unprecedented transition of process methodologies.
These collaborations have focused on risk reduction around critical matters, including system leak integrity, change control management, resin consistency, extractables data, particulates identification and control, workforce training and education and now sustainability in its many iterations.
Based on these problem-solving efforts, SUT adoption continues to evolve as a safe, efficient and affordable bioprocess platform. Furthermore, looking ahead, as current traditional manufacturing systems approach an age where significant equipment re-purchase must be carried out or a line must be upgraded, or a new facility built to improve efficiency or to increase output; transition to single-use manufacturing lines will increase due to the need to produce new drugs or therapies quickly, with the flexibility and speed-to-market benefits that SUT provides. The future is bullish and preparation for new markets and new challenges is key.
The emergence of cell and gene therapy (CGT) markets: new SUT opportunities
And prepare we must. Beside the anticipated continued growth in traditional single-use – ie, large-molecule bioprocessing – on the horizon, there are now new markets for SUTs, as exemplified by the emerging field of CGTs. Much has been written and discussed about CGT promises and challenges. Scalability, automation and cost-minimisation are key drivers prior to commercialisation of CGT (along with regulatory hurdles) and CGT cures will only happen inside of precision plastics systems, which are yet to be invented. These challenges are addressed in a BPSA whitepaper which fully addresses and dissects the technical challenges of scaled CGT manufacture.
To clarify, CGT, as with large-molecule bioprocess, shares patient safety as a firstorder concern, with little margin for error. Patient-specific therapies will re-double the scrutiny needed for particulate control, extractables, leak integrity, operator training, logistics, lead times and process control. Is the SUT supply base ready? Again, if past is prologue, the SUT supply base will again step up to these urgent challenges through collaborative innovation and co-operation, making curative therapies available to the acutely and chronically ill at accessible prices.
Future SUT challenges: the duality of sustainability and post-use disposal
Returning to the ‘S Word’ – sustainability: It’s here to stay. We’re all aware that SUTs are diverse systems inclusive of many types of polymers, silicones and thermo-plastics. There is no question, in a world awash with used plastic in landfills, rivers, oceans and storm systems, that the SUT industry must deal with matters of sustainable corporate practices and sensible disposal of post-use waste, ie, smart disposal.
As a caveat, in our growing market sector there is still no firm number of the pounds or kilos of used plastic that can be tied to SUT production and use. Overall, however, plastics are experiencing an unprecedented public relations drubbing. A quick visit to www.ibanplastic.com (and there are hundreds of similar sites) reveals that one million plastic bottles are bought every minute, 500 million straws are given out every day and an estimated four trillion plastic bags are used worldwide annually, with just 1 percent of them being recycled. None of these statistics are verifiable, but the pictures we have all seen tell the story: harmed wildlife, dirty rivers and Pacific Ocean plastic “gyres.” How much of that is SUT-related? We don’t know, but we hope it is minimal.
To further the challenge, sustainability in SUTs has two elements: the sustainable merits of SUT as employed in a process (ie, sustainable use) and the need for environmentally-sound, post-use disposal (smart disposal).
In terms of sustainable use, SUTs offer clear benefits. Extensive lifecycle analyses (LCA) of plastics versus steel systems have been carried out, which indicate that in many cases, SUTs can lead to a reduction in water depletion, climate change, ozone depletion and human toxicity, among others. When using SUTs there may be a reduction of water for injection, process water and steam, as well as fewer requirements for cleaning and sanitation in place. Consequently, there is a common belief that single-use processes are, in fact, sustainable compared to alternatives. Overall, LCA studies have revealed that single-use process technology is often less environmentally impactful than traditional metal processes, with some exceptions based on a combination of geography and process scale. It is indeed a complicated issue.
In terms of smart disposal, polymeric bioprocess systems are mixes of component polymers, which present a challenge to recyclers. End-of-life options (besides recycling) include landfill, incineration and pyrolysis, each of which offers benefits and problems. So, what are ‘end of life’ options for our waste plastics? Probably a combination of the above. The BPSA has formed a Sustainability Council, which meets bi-monthly to address these issues and expects to publish two guidance documents around sustainability in Q4 of 2019. Please stay tuned and visit our website for further information.
Final perspectives
It has been said that “single-use saves” – it saves time, money, resources and lives. For these compelling reasons, and others, it does appear that SUTs are poised for market growth well into the next decade – provided the industry remains focused on the mission to innovate, invest and collaborate, with an eye on sustainable practices.
About BPSA
The Bio-Process Systems Alliance (BPSA), an affiliate of SOCMA, was formed in 2005 as an industry-led international association dedicated to encouraging and accelerating the adoption of single-use manufacturing technologies used in the production of biopharmaceuticals, cell and gene therapies and vaccines. www.bpsalliance.org.
CONTACT: For more information, e-mail BPSA Executive Director Kevin Ott at kott@socma.org.